
+
Facile à utiliser Brevets Recherche & Annuaire Avocat brevet Ce brevet peut être à vendre ou à louer. Contactez nous Est-ce votre brevet? Cette revendication brevet maintenant. Yacobi et al. "Stress Relief Variations et dans GaAs Pattern.", Appl. Phys. Lett. 52 (7), le 15 fév, 1988, pp. 555-557. Li et al. «Aspects de zones sélectives de croissance.", J. Electrochem. Soc. vol. 130, n ° 10, octobre 1983, pp. 2072-2075. Deppe et al. «Effets de Microfissuration sur. GaAs Quantum Well Lasers sur Si", Appl. Phys. Lett. 53 (10), le 5 septembre 1988, pp. 874-876. Soga et al. «Selective MOCUD croissance de GaAs sur Si.", Jpn. J. Appl. Phys. vol. 26, n ° 2, février 1987, pp. 252-255. Examinateur principal: Chaudhuri; Olik adjoint examinateur: Bunch; William D. Attorney, Agent or Firm: Daniel; William J. revendications 1. Dans un procédé pour déposer une couche de cristaux de GaAs sur un substrat en Si, l'amélioration du contrôle de la formation de microfissures dans ladite couche en confinant ces microfissures à au moins un emplacement prédéterminé dans ladite couche de cristaux par l'étape comprenant avant le dépôt, partiellement recouvrir ledit substrat par un masque en laissant une fenêtre généralement en forme géométriquement sur ledit substrat de silicium à découvert pour un dépôt sur celle-ci de ladite couche de cristal, ledit masque définissant une limite autour de ladite découverte région de fenêtre et comprenant au moins une desdites au moins une pointe acérée emplacement prédéterminé faisant saillie dans ladite région de fenêtre, au moins approximativement dans une direction de clivage des cristaux déposée par la suite de ladite couche de GaAs. 2. Procédé selon la revendication 1, dans lequel ladite région en forme générale géométriquement comporte deux côtés généralement opposés et au moins une paire desdites pointes sont définies par ledit masque, les points de chaque paire étant situés sur deux côtés opposés de ladite région en général, opposé emplacements prédéterminés. 3. Procédé selon la revendication 1, dans lequel ledit masque comprend une partie disposée à l'intérieur de ladite région de fenêtre et au moins un tel point pointu est défini par la partie de masque intérieur. 4. Procédé selon la revendication 1, dans lequel au moins un tel point pointu est situé sur la limite extérieure de ladite zone de fenêtre. 5. Procédé selon la revendication 1, dans lequel ledit masque est obtenu par dépôt de SiO 2 sur ledit substrat en Si suivi par une photolithographie et une gravure chimique humide. 6. Procédé selon la revendication 1, dans lequel GaAs est déposé au moyen de la technique de dépôt chimique en phase vapeur organométallique. 7. Procédé selon la revendication 1, dans lequel, dans une ouverture dans ledit masque dans laquelle du GaAs est déposé une deuxième configuration de masque est prévue avec au moins un tel point pointu dirigé sensiblement dans une direction de clivage de cristaux de GaAs. 8. Dans un procédé de formation d'un dispositif électronique intégré dans au moins une région définie d'une couche de cristaux de GaAs ayant une surface plus grande que ladite zone, laquelle couche est cultivé sur un substrat en Si masqué à une température donnée, puis on refroidit, de sorte que les microfissures sont formées dans ladite couche de GaAs sur un tel refroidissement, l'amélioration de l'induction délibérément la formation de microfissures au niveau d'au moins un emplacement dans ladite couche de GaAs extérieur de chaque telle zone définie au moyen d'au moins un cran aigu créé dans une paroi latérale de ladite couche au moyen d'au moins un point pointu correspondant prévu par ledit masque à au moins un emplacement sous forme espacée de ladite région et étendant approximativement dans une direction de clivage de ladite couche pour initier la formation de microfissures au niveau de ladite défini encoche de sorte que ledit dispositif ne soit pas affectée par la présence de ces microfissures. 9. Procédé selon la revendication 8, dans lequel au moins une paire de ces encoches est créé dans les parois latérales de ladite couche, les encoches de chaque paire étant situés à des emplacements généralement opposés sur lesdites parois latérales de la couche en dehors de ladite zone définie, de sorte que toute microfissures se prolonge entre les sommets des crans d'une telle paire. 10. Procédé selon la revendication 8, dans lequel, avant la croissance de ladite couche de cristaux de GaAs dudit substrat en Si est partiellement couvert par un masque à laisser à découvert une fenêtre dudit substrat en Si entourant ladite région définie pour la réception de ladite couche de cristaux sur celle-ci , ledit masque étant configuré avec une pointe acérée à au moins un locus le long de sa frontière qui les projets de point intérieurement de ladite zone de fenêtre découvert dans une direction de clivage des cristaux de la couche de GaAs ensuite développée pour créer ainsi ladite forte entaille dans la paroi latérale de la couche de GaAs, ledit site étant à l'extérieur de la région définie du dispositif électronique. 11. Procédé selon la revendication 8, dans lequel ledit masque est obtenu par dépôt d'une couche de SiO 2 sur ledit substrat en Si par la suite photolithographie et gravure chimique humide pour éliminer au moins une partie de fenêtre sélectionnée dudit SiO. 2 couche pour exposer au moins une zone sous-jacente dudit substrat pour la réception de celle-ci la couche en GaAs correspondante. 12. Procédé selon la revendication 8, dans lequel au moins une telle encoche forte est créée dans une paroi latérale extérieure de ladite couche de cristaux de GaAs. 13. Procédé selon la revendication 8, dans lequel ladite couche de cristaux de GaAs présente une ouverture intérieure à l'intérieur définissant une paroi latérale intérieure de ladite couche cristalline et au moins une telle encoche forte est créée dans ladite paroi latérale intérieure de ladite couche de cristal. 14. Procédé selon la revendication 8, dans lequel GaAs est déposé au moyen de la technique de dépôt chimique en phase vapeur organométallique. 15. Procédé selon la revendication 8, dans lequel, dans une ouverture dans ledit masque dans laquelle du GaAs est déposé une deuxième configuration de masque est prévue avec au moins un tel point pointu dirigé sensiblement dans une direction de clivage de cristaux de GaAs. 16. Procédé pour contrôler la formation d'une couche de cristaux de GaAs déposée sur une position prédéterminée généralement en forme géométriquement zone de fenêtre d'un substrat de silicium masqué de microfissures provoquée au cours du refroidissement après ledit dépôt par des différences dans le coefficient de dilatation thermique de ladite couche et le substrat, qui comprend la formation au moyen d'un point pointu fourni par ledit masque à au moins un locus le long des parois latérales de ladite couche de cristaux GaAs une entaille nette étendant vers l'intérieur dirigé sensiblement le long d'une direction de clivage de la forme de ladite couche de GaAs, selon laquelle un tel microfissure provient à la point d'un tel cran. 17. Procédé selon la revendication 16, dans lequel une telle entaille est prévue à chacune d'au moins une paire de loci généralement opposés sur les parois latérales de ladite zone de couche de forme, de sorte que toute microfissures se prolonge entre le point d'encoches à de telles paires opposées de locus. 18. Procédé selon la revendication 16, dans lequel ladite couche de GaAs de forme a une ouverture intérieure à l'intérieur définissant une paroi latérale intérieure de ladite couche cristalline et au moins une telle encoche forte est créée dans ladite paroi latérale intérieure de ladite couche de cristal. 19. Procédé selon la revendication 16, dans lequel au moins une telle encoche forte est créée dans une paroi latérale extérieure de ladite couche de cristal. La description CONTEXTE DE L'INVENTION 1. Domaine de l'invention La présente invention a pour objet l'intégration de GaAs sur un substrat en Si. L'invention se rapporte plus particulièrement à l'intégration monolithique des structures électroniques ou optoélectroniques GaAs / AlGaAs tels que des diodes électroluminescentes sur un substrat en Si sur lequel Si de circuits électroniques tels que les conducteurs de LED (transistors à effet de champ) peut également être intégré. 2. Description de l'art antérieur (couches GaAs ou GaAs structures, à savoir GaAs / AlGaAs diodes électroluminescentes peuvent être cultivées sensiblement exempt de contraintes sur le dessus d'un substrat Si, habituellement sous forme de plaquette, à haute température, à savoir 700.degree. C . Toutefois, pendant la période de refroidissement hors du rétrécissement différent de GaAs et Si, provoque des contraintes dans les matériaux. Ces contraintes peuvent provoquer la plaquette de se plier lorsque l'épaisseur de la couche GaAs de croissance sur le substrat en Si est relativement faible, par exemple lorsque cette épaisseur ne dépasse pas 3 micromètres. Si la couche de GaAs est plus épais, les microfissures peuvent apparaître dans la structure de couche épitaxiale sur la plaquette. La présence de contraintes matérielles affecte négativement les propriétés électriques et / ou optiques des dispositifs GaAs / Si. gauchissement matériau empêche la lithographie et le traitement ultérieur de la tranche. Les microfissures se produisent de façon aléatoire peuvent également interférer avec le bon fonctionnement des dispositifs électroniques qui sont finalement formés. Les problèmes ci-dessus qui se posent lors de la croissance de GaAs couches sur des substrats de silicium sont décrits dans les publications suivantes: «variations de stress en raison de microfissures dans GaAs sur Si" publiées par B. G. Yacobi et al. dans Appl. Phys. Lett. Vol. 51, n ° 26 et "variations de stress et secours en GaAs motifs cultivés sur des substrats dépareillées» par B. G. Yacobi et al. dans Appl. Phys. Lett. Vol. 52, n ° 7. Quelques solutions ont été proposées dans la technique pour remédier aux problèmes ci-dessus. Dans Appl. Phys. Lett. Vol. 53, n ° 3 un document sur "Le gauchissement de GaAs-sur-Si wafers et sa réduction par la croissance sélective de GaAs à travers un masque d'ombre de silicium par épitaxie par faisceau moléculaire" a été publié. Le gauchissement entièrement recouvertes de plaquettes de GaAs-Si et de Si gaufrettes ayant une croissance sélective de GaAs (obtenue en utilisant un masque d'ombre Si) ont été étudiés. Une réduction significative de gauchissement est observée en limitant la zone de GaAs de croissance. Il est également connu de munir la face arrière du substrat de silicium avec un film afin de contrecarrer les contraintes qui sont induites par la couche épitaxiale de GaAs. RESUME DE L'INVENTION Il est un objet de la présente invention est de fournir méthode de GaAs de croissance sur un substrat en Si qui permet d'obtenir une réduction des contraintes dans le stratifié final résultant de la différence des coefficients de dilatation thermique de ces matériaux pendant le refroidissement. Un autre but de l'invention est de fournir un procédé de croissance de GaAs sur un substrat en Si à la suite de laquelle des tranches planes (plats) sont obtenus de telle sorte que les opérations lithographiques ultérieures ne sont pas entravés. Encore un autre objet de la présente invention est de proposer un procédé d'intégration d'un dispositif électronique ou opto-électroniques de GaAs sur un substrat en Si de sorte qu'aucun micro-fissures se produisent à l'intérieur de la zone active des appareils. D'autres objets apparaîtront à la lecture de la description ci-après. La présente invention concerne un procédé de formation d'un dispositif électronique intégré ou d'une partie de celle-ci par la croissance de GaAs sur un substrat de Si à une température donnée et le refroidissement consécutif du substrat, caractérisé en ce que des microfissures sont induites intentionnellement dans ladite couche de GaAs à des endroits où le fonctionnement dudit dispositif ou une partie de celui-ci ne sont pas affectées. Par microfissures intentionnellement créées dans les régions inopérantes d'un dispositif intégré selon la présente invention, les contraintes dans les matériaux peuvent être réduits et l'apparition de microfissures à des endroits aléatoires peuvent être évités Pour atteindre les microfissures ci-dessus à des endroits où le fonctionnement des dispositifs ou une partie de celui-ci ne soit pas affectée, une partie du substrat est recouverte d'un masque avant le dépôt de GaAs. Le masque est de préférence un masque de SiO2. Il a été constaté qu'en utilisant une topographie spécifique ou la configuration du masque (comme cela sera expliqué plus loin en se référant aux dessins) microfissures peuvent être induites à des emplacements voulus prédéterminés. Par l'utilisation d'un masque muni d'au moins un sommet ou un point dirigé dans une direction de clivage de cristaux de GaAs, des microfissures sont induites dans la couche monocristalline initiation à partir dudit sommet et se propageant dans ladite direction de clivage. Ainsi, la présente invention fournit en outre généralement un procédé de formation de microfissures à des endroits prédéterminés dans une couche de GaAs cultivées sur un substrat en Si, caractérisé en ce qu 'avant la croissance de ladite couche de GaAs dudit substrat de Si est partiellement couvert par un masque, ledit masque étant conçu (en forme) avec au moins un sommet soit une pointe acérée projetant intérieurement, au moins approximativement dans une direction de clivage des cristaux de ladite couche de GaAs. Une topographie du masque, et plus précisément l'emplacement et le nombre de sommets ainsi créées peuvent être sélectionnés de telle sorte que les microfissures peuvent être délibérément induite à des emplacements prédéterminés. Un soi-disant sommet agit en réponse à des contraintes mécaniques appliquées comme un coin qui clive le cristal GaAs et donc est aussi appelé «coin». Dans une première étape SiO 2 est déposée par exemple par plasma de dépôt chimique en phase vapeur (PECVD) sur le substrat de Si. Les régions de la couche de SiO 2 sont à nouveau éliminés par photolithographie et gravure chimique humide de manière à former un masque. Ensuite, sur la résultante partiellement enrobées GaAs de substrat de silicium est déposé par exemple au moyen de la technique de dépôt chimique en phase vapeur organométallique (MOVCD), qui est connu dans la technique. Selon cette technique GaAs est déposé sur Si dans un quartzreactor. La source triméthylgallium organométallique (CH3) 3 Ga peut par exemple être utilisé pour transporter un composant du groupe III, à savoir. Ga, utilisant l'hydrogène comme gaz porteur. Arsine peut être utilisé pour le transport de l'élément V du groupe As. Hydrogenselenide peut être utilisé pour obtenir un dopage de type n et de diéthylzinc (transport de vapeur d'hydrogène) peut être utilisé pour obtenir de type p dopage. Les sources ci-dessus sont chauffés dans un quartzreactor. Par la réaction pyrolytique simplifiée suivante à 700.degree. C GaAs est déposé sur un substrat en Si présente dans le réacteur. La morphologie de GaAs qui est déposée dépend, entre autres, sur les caractéristiques du matériau sous-jacent. Monocristallin GaAs est obtenu sur la zone non revêtue Si alors que sur le SiO2 GaAs masque polycristallins dépôt se trouve. En utilisant une configuration de masque spécifique créant coupants encoches dans les régions de couche déposée selon la présente invention, lors du refroidissement, des microfissures sont introduits dans le GaAs monocristallin initiant des sommets et se propageant dans au moins une direction de clivage. Aucun des microfissures se trouvent dans d'autres régions de la couche. DESCRIPTION BRÈVE DES DESSINS Pour une meilleure compréhension de la présente invention et des modes de réalisation préférés, il est fait référence à la description détaillée faite ci-après en relation avec les dessins ci-joints et d'images, dans lequel FIGUE. La figure 1 représente schématiquement la topographie d'une diode GaAs / AlGaAs d'émission et d'un transistor à effet de champ (MOSFET) qui sont intégrés de manière monolithique sur un substrat en Si, FIGUE. 2 est une photographie reproduite montrant un provenait spontanément et au hasard microfissure, FIGUE. La figure 3 illustre schématiquement les emplacements des microfissures intentionnellement induits sur un substrat sur lequel des dispositifs électroniques ou optoélectroniques sont cultivées, FIGUE. La figure 4 illustre l'utilisation d'un masque de SiO 2 et la croissance de GaAs sur la plaquette, FIGUE. La figure 5 représente un masque qui peut être utilisé pour l'obtention de micro-fissures induites délibérés, FIGUE. 6 est une photographie reproduite montrant microfissures induites, FIGUE. 7 et 8 illustrent différents types de masques, FIGUE. La figure 9 est une représentation agrandie de formes différentes de sommets, FIGUE. 10-13 illustrent les résultats d'expériences réalisées sur la formation de fissures. FIGUE. La figure 1 montre un exemple d'un dispositif qui est composé d'un premier composant qui est un circuit de Si plus précisément un transistor à effet de champ 2 et un second composant qui est un composant de GaAs, à savoir une diode émettrice de lumière 3. Les deux composants sont intégrés sur une commune substrat de silicium 1. diode électroluminescente 3 comporte 5 couches développées sur le dessus de l'autre. Sur le substrat de silicium une couche tampon en GaAs est d'abord cultivé. Au-dessus de ladite couche tampon en GaAs, une couche de revêtement en AlGaAs, une couche de GaAs actif ou AlGaAs, une seconde couche de revêtement en AlGaAs, et enfin une couche de contact en GaAs sont cultivés. FIGUE. La figure 2 représente une microfissure aléatoire qui est pris naissance spontanément dans une structure de couches GaAs / AlGaAs déposée sur un substrat en Si. Malheureusement, cette microfissure traverse la partie opérationnelle de la diode électroluminescente GaAs et rend le dispositif inutilisable (photographie prise au moyen d'un microscope électronique). A cause de différents retrait de GaAs et Si au cours de la période de refroidissement de la température à laquelle GaAs est cultivé sur le substrat Si à la température de fonctionnement (température ambiante), microfissures, comme illustré par cette reproduction photographie peut provenir à des endroits aléatoires et peut ruiner la le fonctionnement du dispositif. Ce problème est résolu par le procédé de la présente invention selon lequel des microfissures sont volontairement créées de telle sorte que les contraintes du matériau sont réduites et que la position exacte des microfissures peuvent être contrôlés de manière à empêcher la génération d'une microfissure dans une région importante pour l'exploitation à l'intérieur un dispositif. FIGUE. La figure 3 illustre que les microfissures peuvent être créés sur des endroits à l'extérieur des zones actives des dispositifs. FIGUE. La figure 3 représente schématiquement une série de diodes électroluminescentes 4, 5, 6 et 7 intégrés sur un substrat commun. Les lignes tracées numérotés 8-13 représentent les emplacements sur lesquels les microfissures peuvent par exemple être formés en dehors des dispositifs de manière à ne pas affecter leur fonctionnement. Afin d'obtenir ledit microfissures aux endroits qui ne nuisent pas à l'opération de l'appareil de la procédure suivante est suivie. Le substrat de silicium (14) est tout d'abord recouverte par un masque, de préférence un masque de SiO 2 (15), au moyen d'un dépôt de SiO 2 comme cela est connu sur le substrat en Si (fig. 4) et l'enlèvement de une région de la couche de SiO 2 par photolithographie et gravure chimique humide. Ensuite, le GaAs est déposé sous forme d'une couche. La Fig. 4 la morphologie différente de GaAs sur différentes régions de surface est représentée. La morphologie de GaAs déposée sur les régions de SiO 2 est polycristalline (16), tandis que sur les régions de Si-substrat (non couvert par SiO 2), il est monocristallin (17). Ce qui suit est une description d'une procédure spécifique de formation d'un masque selon la présente invention. Le masque utilisé dans les expériences décrites plus loin ont été obtenus en utilisant cette procédure particulière. Les couches de masquage peuvent être par exemple plasma déposé sur Si-wafers (p. sup.-, (100) + 3 ° C. Vers perpendiculaire [0 1 1] direction) en utilisant Enhanced Plasma Chemical Vapor Deposition. Selon un mode de réalisation préféré de la présente invention, les plaquettes sont nettoyées dans un mélange de HF et d'une solution à 50% d'eau DI deionisised (1 partie / 19 parties) pendant 15 secondes avant le processus de dépôt. Ensuite, les pastilles sont chargées dans la chambre à vide d'un système PD80 (technologie de plasma). Les paramètres du procédé de déposition conduisant à une vitesse de 33 nm / min et le dépôt d'une couche de 100 nanomètres dépôt, sont les suivantes: la pression totale dans la chambre: 500 mTorr, température de l'échantillon: 300.degree. C. RF-fréquence: 100 kHz, gasflow: 10 sccm SiH4, 120 sccm N2O, Pour le motif de la SiO2 - layers un processus de photolithographie standard est utilisé. Les plaquettes sont nettoyées dans des solvants bouillant dans soxhlets (15 min trichloréthylène, 15 min dans de l'acétone, 15 min dans de l'alcool isopropylique). Ensuite, les plaquettes sont rincées dans de l'eau désionisée (DI) et séchés à l'air à une température de 120.degree. C pendant 30 min. Après séchage, les échantillons sont spincoated (3000 tours par minute, 40 secondes) en résine photosensible. Pour ces expériences, AZ1350 résist (Shipley) est utilisé. Le resist est cuit pendant 5 min dans un four chaud plaque à 90.degree. C dans une atmosphère d'azote. Le résist est ensuite exposé aux UV (haute pression de mercure lampe) dans un masque d'alignement à travers un masque tel que représenté sur la Fig. 7. (Durée d'exposition: 34 sec) Les zones exposées sont développées. (Développeur: diluée AZ 2401 développeur (Shipley), dilution: 1 partie AZ 2401, 4 parties DI, le temps de développement: 30 sec). Avec la résine photosensible comme un masque, la couche iL de SiO 2 est éliminée par attaque chimique. (Solution de gravure: BHF de Transene, gravure pendant 50 sec). L'étape suivante est la croissance épitaxiale de GaAs en tant que couche au moyen du procédé de dépôt chimique en phase vapeur organométallique (dans un système Epitor 04 Thomas Swan). Le réacteur utilisé accueille quatre sources organométalliques et trois hydrures. En tant que gaz porteur de l'azote (inerte) et de l'hydrogène purifié Pd peuvent être sélectionnés par un soufflet étanche vannes pneumatiques. bains à température contrôlée sont inclus dans chaque ligne organométallique. Le débit de gaz dans chaque conduite est commandée par MKS régulateurs de débit massique. Le système est équipé d'une commutation rapide EPIFOLD collecteur de gaz pour le dépôt des interfaces abruptes. La croissance peut être commandée manuellement ou par ordinateur. Le réacteur est un quartzreactor horizontal avec une section transversale rectangulaire et travaillant à la pression atmosphérique. Pendant la croissance, les substrats pondent au-dessus d'une section rectangulaire Si-suscepteur qui est chauffé par une lampe infrarouge (1000 W, 110 V). La température est mesurée au moyen d'un thermocouple placé dans le suscepteur à Si et par un régulateur PID du lamppower est ajustée en continu. Les sources disponibles sont triméthylgallium (TMG), triméthylaluminium et diéthylzinc les organométalliques et 5% AsH. sub.3 (arsine) dans l'hydrogène, 200 ppm SiH4 (silane) et 200 ppm H2S Se (hydrogène séléniure), à la fois dilué dans l'hydrogène. conditions de croissance normales sont T. sub. gr = 660.degree. C la vitesse de croissance = 100 nm / min, la fraction molaire (TMG) = 2.10.sup.-4, la fraction molaire (AsH. sub.3) = 2.10.sup.-3. De préférence, une étape de préparation du substrat pour la croissance de GaAs sur Si est comprise. Cette étape consiste à une procédure de gravure ex situ de 15 sec dans un HF: DI 01h19 mélange suivi d'un rinçage sous un courant DI (18,03 MOhm) pendant 60 secondes et en soufflant sec dans l'écoulement de N2. (Solution de HF: 49% -51%). Après l'in situ étuvage, le substrat est refroidi à 450.degree. C et le débit du gaz vecteur H2 est portée à 4,4 1 / min. Lorsque la température est stabilisée à 450.degree. C, le milieu de croissance est rincée avec 200 cc / min AsH. sub.3 (5% de H2) pendant l'écoulement à 2 min. Immédiatement après cette opération de gravure, le substrat est chargé dans le réacteur. La préparation substrat in situ consiste en une procédure de étuvage à 950.degree. C sous un flux de H2 1 1 / min pendant 1 heure. Immédiatement au-delà du flux de triméthylgallium est commuté vers le réacteur et une couche de formation de germes de GaAs minces (environ 10 nanomètres) est cultivé pendant 60 secondes. En vertu d'un AsH. sub.3 écoulement continu du point de consigne du chauffage du réacteur est fixé à 720.degree. Au bout de 5 min. la valeur de lecture de la température étant d'environ 700.degree. C. le point de mettre progressivement diminué à 660.degree. C (température de croissance normal). Après un supplément de 5 min, la valeur de lecture de la température étant stabilisée à 660.degree. C, la croissance de la structure GaAs / AlGaAs voulu est démarré. Le dépôt sur la paroi de quartz-réacteur doit être éliminé après chaque cycle de croissance de GaAs sur Si. Afin d'empêcher la désorption de ce dépôt une surpression de AsH. sub.3 est nécessaire lors de l'étape in situ étuvage pour la préparation de substrat du deuxième cycle de croissance de GaAs sur Si. Aux températures élevées nécessaires (950.degree. C.), les fissures AsH. sub.3 trop vite pour que le filtre à poussière à la sortie du réacteur s'engorge et finalement provoque une pression accumulée dans le milieu de croissance. À chaque croissance exécuter le réacteur de quartz est retirée du système et remplacée par une propre. Le premier réacteur et le suscepteur sont ensuite gravés dans l'eau régale, on les rince à déborder Di et dans l'alcool isopropylique. Après un étuvage pendant plusieurs heures à 100.degree. C dans un four à vide, l'ensemble réacteur-suscepteur est remplacé dans le système et on le chauffe jusqu'à 850.degree. C sous un courant de H2 de 2,2 1 / min pendant au moins une heure. Le réacteur gravé est prêt pour la course de croissance suivante de GaAs sur Si. Pour la création intentionnelle de microfissures sur des emplacements spécifiques (où aucun dispositif opératoire sont présents), la configuration du masque de SiO2 est d'une importance particulière. A cet effet, le masque SiO2 définit au moins un sommet à-dire le point ou l'angle, orienté vers une direction de clivage du cristal GaAs (à savoir le [0 1 1] ou [0 1 1] direction). Dans un mode de réalisation particulier, chaque sommet est symétrique par rapport à une telle direction. Un exemple d'un tel masque est représenté sur la Fig. 5. La partie ombrée représente le substrat couvert par un masque de SiO2. A l'intérieur de la frontière du masque de SiO 2 sur le substrat à découvert (également appelée fenêtre), les dispositifs électroniques actifs peuvent être fabriqués. Vertex (par exemple étant indiqués par les chiffres 18 et 19) à la périphérie du SiO 2 - mask autour de la fenêtre sont dirigées vers une direction de clivage des cristaux à-dire vers l'intervalle [0 1 1] ou [0 1 1 ] direction. En conséquence desdits sommets dans la périphérie du masque, des microfissures apparaissent dans des endroits déterminés dans la couche de GaAs déposé dans l'ouverture du masque. Ces microfissures se prolongent dans les directions de clivage du cristal (représenté par les lignes en pointillés sur la Fig. 5). Les microfissures diminuent la mécanique (refroidissement) dans les contraintes matérielles, d'une part, mais ne pas affecter le fonctionnement de l'appareil depuis leur emplacement est sensiblement fixe et des dispositifs peut être fabriqué localement afin que ces microfissures sont situés en dehors des zones actives sur le plan opérationnel. FIGUE. 5 représente une possible topographie de masque. D'autres configurations sont possibles, d'autres exemples sont illustrés sur les Fig. 7 et 8. Il est clair que au moins un sommet ou une encoche dirigés dans les cristaux direction clivage est nécessaire pour obtenir les microfissures induites contrôlées selon la présente invention. FIGUE. 6 est une photographie reproduite montrant un substrat Si partiellement couvert par un masque SiO2 20 ayant des frontières plus ou moins en zigzag définissant des sommets ou des angles pluriel. Microfissures s'étendent d'un sommet à un sommet opposé. Les microfissures étendent dans la direction de clivage du cristal. Microfissures (lignes verticales très fines sur la photographie reproduite) sont par exemple indiqué par les chiffres 21 et 22. FIGUES. 7 et 8 illustrent différents types de masques, les dimensions sont exprimées en micromètres. FIGUE. 7a, b et c représentent des masques dont les sommets ont la même forme et le même emplacement, seule la largeur de l'ouverture (ou fenêtre) dans le masque est modifié. L'influence de l'espacement des différents sommets peuvent également être analysées au moyen de ce masque. La distance entre les sommets varie entre 50 micromètres et 500 micromètres, la largeur de la fenêtre varie entre 100 et 500 micromètres. FIGUES. 7d, figures. 8 E et F illustrent des masques dont les sommets sont situés sur différents côtés (côtés opposés ainsi que des côtés perpendiculaires) de la fenêtre dans le masque. La Fig. 8e la forme des sommets est également modifiée. FIGUES. 8l et k représentent des masques ayant des sommets d'un côté, les sommets sont équidistants. La Fig. 8l, la forme des sommets ne sont pas identiques. FIGUES. 8g et j représentent des masques dans lesquels plusieurs configurations différentes de sommets sont formés dans les parties centrales respectives de l'ouverture dans le masque (forme de croix, linéaire ou sous forme de fente, en forme de losange-). FIGUE. La figure 9 est une représentation agrandie de formes différentes de sommets. L'angle varie d'environ 20.degree. à environ 60.degree. Une autre forme d'un sommet est également représenté. Les résultats des expériences sur la formation de fissures sont présentés dans les photographies reproduites 10 et 13. Dans la croissance successive fonctionne couches de GaAs d'épaisseurs différentes ont été déposées sur le substrat p-Si en utilisant un masque défini dans une couche de SiO2 d'épaisseur de 100 nanomètres. La formation de fissures après le refroidissement du substrat à partir de la température de croissance jusqu'à la température ambiante et le déchargement a été étudiée au moyen d'un microscope à interférence Nomarsky. Les fissures sont visibles lorsque donc observé que des lignes très fines dans les zones monocristallines. Les structures cultivées ont également été plongés dans l'azote liquide (77K) pendant 30 secondes à regarder la propagation éventuelle de la formation de fissures dues à l'amélioration de déformation thermique à ces basses températures. Les fissures sont accentuées et mieux révélées par une très courte gravure dans un H 2 SO 4: H 2 O 2: H2O mélange. Dimensions sur les photographies reproduites correspondent aux dimensions identifiées sur les dessins de masque des figures. 7 et 8. photo Reproduit 10 montre un GaAs épais structure de 6 micromètres (structure inférieure). Le masque utilisé est représenté sur la figure. 8k et 8l. La formation des fissures commence à partir des sommets ou des encoches et se poursuit dans la direction de clivage. Les fissures sont parallèles. Fissures pas lancer d'un sommet (à savoir initier spontanément) ne sont pas trouvés. photo Reproduit 11 montre un autre 6 micromètres d'épaisseur GaAs structure. Le masque utilisé est représenté sur la figure. 8f. Cracks originaires aux sommets situés au même niveau ou un côté parallèle du masque sont parallèles tandis que les fissures provenant des sommets sur les côtés perpendiculaires sont perpendiculaires les unes aux autres. Une légère désorientation constante (désalignement) d'environ 3.degree. on peut le voir entre les fissures et les bords du masque. Ceci résulte d'une désorientation des échantillons Si rectangulaires créés quand ils ont été sciés. Par conséquent, les fissures induites à partir des sommets situés sur les côtés opposés du substrat ne correspondent pas exactement à l'autre. photographies Reproduit 12 montre des fissures formées sur un 3 micromètre GaAs d'épaisseur la structure, tandis que la photographie reproduit 13 présente des fissures formées sur une structure de 6 micromètres. La même configuration de masque (cfr 8e.. FIG) a été utilisé pour les deux structures. Les fissures montrent le même comportement que celui décrit ci-dessus. Le nombre de fissures traversant toute la zone monocristalline est cependant plus élevée dans une structure épaisse de 6 micromètres d'épaisseur dans une structure de 3 micromètres. Etant donné que le masque de la Fig. 8e est utilisé pour obtenir le résultat de photographies reproduites 12 et 13, l'influence de la forme du sommet peut également être étudié sur ces photographies reproduites. Aucune relation constante entre la forme de sommets et de la formation de fissures résultant est mis en place dans ces expériences de croissance. Des expériences ont également montré qu'aucune relation particulière existe entre la interspacing des sommets et la formation de microfissures. Des expériences utilisant des masques des figures. 8g à j montrent que les angles vifs de masque dans le milieu de la zone de croissance induisent également des fissures dans la couche épitaxiale (pas de photographies reproduites). Les masques de la figure. 8g, i et j induire des microfissures dans deux directions perpendiculaires, alors que par le biais du masque de la figure. 8H, microfissures sont induits dans une seule direction de clivage (microfissures proviennent du point angulaire forte). Par conséquent, des expériences ont établi que les microfissures peuvent être introduits dans la couche de GaAs sur un substrat en Si d'une manière contrôlée, à savoir à des emplacements prédéterminés. Les microfissures proviennent de sommets dans un masque et ne se trouvent pas sur d'autres endroits. La distance entre les cales ne montre pas beaucoup d'influence. La génération de microfissures est généralement insensible à la forme des sommets et l'utilisation de cales opposées perpendiculaires les résultats dans les microfissures perpendiculaires. Variation de l'épaisseur de la couche influe sur la densité de microfissures. Aussi croix, linéaires et rhomb formations isolées au milieu du masque-fenêtre peut générer des microfissures. Déposer une demande de brevet Protégez votre idée - Ne laissez pas quelqu'un d'autre premier fichier. Apprendre encore plus. 3 étapes faciles - Remplissez le formulaire, l'application d'examen, et Fichier. Voir notre processus. Attorney Review - Demandez à votre demande examinée par un procureur de brevets. Voir ce qui est inclus.
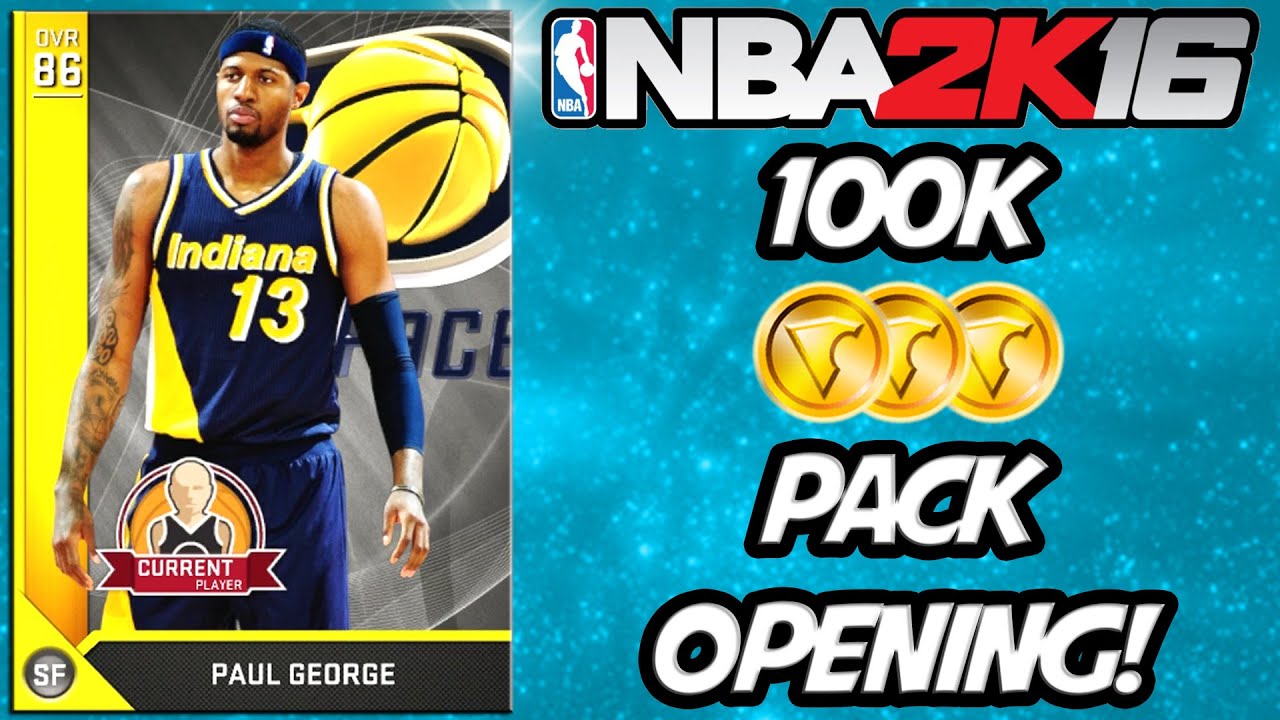
No comments:
Post a Comment